Common Production Processes for Sliding Resistors
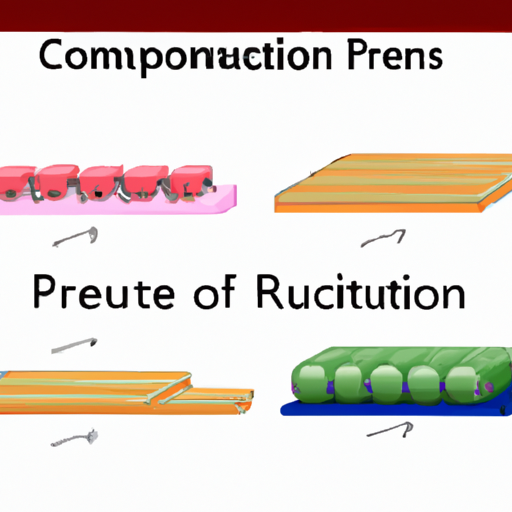
I. Introduction
Sliding resistors, also known as variable resistors or rheostats, are essential components in various electronic applications. They allow for the adjustment of resistance in a circuit, enabling control over current flow and voltage levels. This versatility makes them invaluable in devices ranging from audio equipment to industrial machinery. Understanding the production processes behind sliding resistors is crucial for appreciating their role in electronics and for manufacturers aiming to optimize their production methods.
II. Types of Sliding Resistors
Sliding resistors come in several types, each suited for specific applications:
A. Carbon Composition Sliding Resistors
These resistors are made from a mixture of carbon and a binding material. They are known for their affordability and are commonly used in low-power applications. However, they can be less stable than other types under varying environmental conditions.
B. Wire-Wound Sliding Resistors
Wire-wound resistors consist of a metal wire wound around a core. They are highly accurate and can handle higher power levels, making them suitable for applications requiring precision and durability.
C. Film-Type Sliding Resistors
Film-type resistors are made by depositing a thin layer of resistive material onto a substrate. They offer excellent stability and are often used in high-frequency applications due to their low inductance.
D. Other Specialized Types
There are also specialized sliding resistors designed for specific applications, such as potentiometers used in audio equipment or precision resistors for laboratory settings.
III. Materials Used in Production
The production of sliding resistors involves various materials, each chosen for its specific properties.
A. Conductive Materials
1. **Carbon**: Used primarily in carbon composition resistors, carbon provides a cost-effective solution for low-power applications.
2. **Metal Wires**: Typically used in wire-wound resistors, metals like copper or nickel are chosen for their excellent conductivity and durability.
3. **Conductive Films**: Thin films of conductive materials are used in film-type resistors, offering precision and stability.
B. Insulating Materials
1. **Plastics**: Commonly used for housing and insulation, plastics are lightweight and cost-effective.
2. **Ceramics**: Used in high-temperature applications, ceramics provide excellent insulation and thermal stability.
C. Other Components
1. **Connectors**: Essential for integrating resistors into circuits, connectors must be reliable and conductive.
2. **Housing Materials**: The outer casing of sliding resistors protects internal components and ensures durability.
IV. Common Production Processes
The production of sliding resistors involves several key processes, each critical to ensuring quality and performance.
A. Design and Prototyping
1. **Initial Design Considerations**: The design phase involves determining the specifications, such as resistance range, power rating, and physical dimensions.
2. **Prototyping Methods**: Rapid prototyping techniques, such as 3D printing, can be employed to create initial models for testing and evaluation.
B. Material Preparation
1. **Sourcing Raw Materials**: Manufacturers must establish reliable sources for high-quality conductive and insulating materials.
2. **Pre-processing of Materials**: This may involve cutting, grinding, or treating materials to prepare them for fabrication.
C. Fabrication Techniques
1. **Carbon Composition Process**:
- **Mixing and Molding**: The carbon and binder are mixed and molded into the desired shape.
- **Curing**: The molded resistors are cured to harden the material and enhance stability.
2. **Wire-Wound Process**:
- **Winding the Wire**: A precise amount of metal wire is wound around a core to achieve the desired resistance.
- **Mounting and Securing**: The wound wire is mounted onto a substrate and secured to prevent movement.
3. **Film Deposition Process**:
- **Thin-Film Application**: A thin layer of resistive material is deposited onto a substrate using techniques like sputtering or chemical vapor deposition.
- **Etching and Patterning**: The deposited film is etched to create the desired resistance pattern.
D. Assembly
1. **Component Integration**: All components, including the resistive element and housing, are assembled to create the final product.
2. **Quality Control Measures**: Rigorous quality checks are performed to ensure that each resistor meets specified standards.
E. Testing and Calibration
1. **Electrical Testing**: Each resistor undergoes electrical testing to verify its resistance value and performance under load.
2. **Performance Calibration**: Adjustments may be made to ensure that the resistor operates within the desired parameters.
F. Packaging and Distribution
1. **Packaging Methods**: Resistors are packaged to protect them during transport and storage, often using anti-static materials.
2. **Distribution Channels**: Manufacturers must establish efficient distribution channels to deliver products to customers promptly.
V. Quality Assurance in Production
Quality assurance is a critical aspect of sliding resistor production, ensuring that products meet industry standards and customer expectations.
A. Standards and Certifications
Manufacturers often adhere to international standards, such as ISO 9001, to ensure consistent quality in their production processes.
B. Testing Protocols
Comprehensive testing protocols are established to evaluate the performance and reliability of sliding resistors throughout the production process.
C. Continuous Improvement Practices
Manufacturers implement continuous improvement practices, such as Six Sigma or Lean Manufacturing, to enhance efficiency and reduce waste.
VI. Challenges in Production
The production of sliding resistors is not without its challenges.
A. Material Sourcing Issues
Sourcing high-quality materials can be difficult, especially in times of supply chain disruptions or fluctuations in material prices.
B. Technological Advancements
Keeping up with rapid technological advancements requires manufacturers to invest in new equipment and training for their workforce.
C. Environmental Considerations
Manufacturers must also consider the environmental impact of their production processes, striving to minimize waste and reduce their carbon footprint.
VII. Future Trends in Sliding Resistor Production
The future of sliding resistor production is likely to be shaped by several trends.
A. Innovations in Materials
Research into new materials, such as nanomaterials or advanced composites, may lead to the development of more efficient and durable sliding resistors.
B. Automation and Smart Manufacturing
The integration of automation and smart manufacturing technologies can enhance production efficiency and reduce labor costs.
C. Sustainability Practices
As environmental concerns grow, manufacturers are increasingly adopting sustainable practices, such as recycling materials and reducing energy consumption.
VIII. Conclusion
Sliding resistors play a vital role in the functioning of various electronic devices, making their production processes essential to the electronics industry. From the initial design and material preparation to fabrication, assembly, and quality assurance, each step is crucial in ensuring the reliability and performance of these components. As technology continues to evolve, manufacturers must adapt to new challenges and embrace innovations that will shape the future of sliding resistor production. By focusing on quality, efficiency, and sustainability, the industry can continue to meet the demands of an ever-changing market.